Grafit er et almindeligt ikke-metallisk materiale, sort, med høj og lav temperaturbestandighed, god elektrisk og termisk ledningsevne, god smøreevne og stabile kemiske egenskaber; god elektrisk ledningsevne, kan bruges som elektrode i EDM. Sammenlignet med traditionelle kobberelektroder har grafit mange fordele såsom høj temperaturbestandighed, lavt afladningsforbrug og lille termisk deformation. Det viser bedre tilpasningsevne i bearbejdning af præcisions- og komplekse dele og store elektroder. Det har gradvist erstattet kobberelektroder som elektriske gnister. Hovedstrømmen inden for bearbejdningselektroder [1]. Derudover kan slidstærke grafitmaterialer bruges under højhastigheds-, højtemperatur- og højtryksforhold uden smøreolie. Meget udstyr bruger i vid udstrækning grafitmateriale til stempelkopper, tætninger og lejer.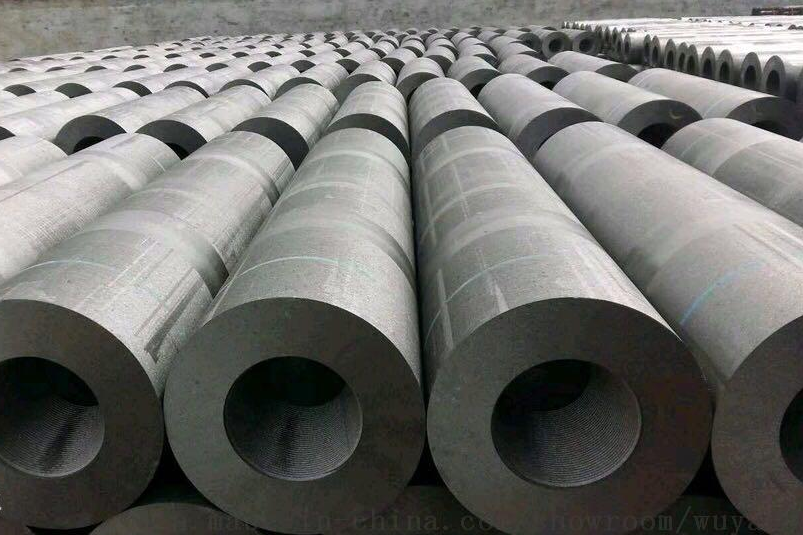
I øjeblikket anvendes grafitmaterialer i vid udstrækning inden for maskiner, metallurgi, kemisk industri, nationalt forsvar og andre områder. Der findes mange typer grafitdele, komplicerede delestrukturer, høje dimensionsnøjagtigheder og krav til overfladekvalitet. Indenlandsk forskning i grafitbearbejdning er ikke dybdegående nok. Indenlandske grafitbearbejdningsmaskiner er også relativt få. Udenlandsk grafitbearbejdning bruger primært grafitbearbejdningscentre til højhastighedsbearbejdning, hvilket nu er blevet den vigtigste udviklingsretning for grafitbearbejdning.
Denne artikel analyserer hovedsageligt grafitbearbejdningsteknologi og bearbejdningsmaskiner ud fra følgende aspekter.
①Analyse af grafitbearbejdningsydelse;
② Almindeligt anvendte grafitforarbejdningsteknologiske foranstaltninger;
③ Almindeligt anvendte værktøjer og skæreparametre ved bearbejdning af grafit;
Analyse af grafitskæringsydelse
Grafit er et sprødt materiale med en heterogen struktur. Grafitskæring opnås ved at generere diskontinuerlige spånpartikler eller pulver gennem sprødbrud i grafitmaterialet. Med hensyn til skæremekanismen for grafitmaterialer har forskere i ind- og udland udført en masse forskning. Udenlandske forskere mener, at grafitspåndannelsesprocessen omtrent sker, når værktøjets skærkant er i kontakt med emnet, og værktøjets spids knuses, hvilket danner små spåner og små huller, og der dannes en revne, som vil strække sig til forsiden og bunden af værktøjsspidsen og danne en brudhul, og en del af emnet vil blive brudt på grund af værktøjets fremføring og danne spåner. Indenlandske forskere mener, at grafitpartiklerne er ekstremt fine, og værktøjets skærkant har en stor spidsbue, så skærekantens rolle ligner ekstrudering. Grafitmaterialet i værktøjets kontaktområde - emnet - presses af spidsens rilleflade og værktøjets spids. Under tryk produceres sprødbrud, hvorved der dannes spån [3].
Under grafitskæringsprocessen forårsages der en vis påvirkning af grafitemnet på grund af ændringer i skæreretningen for emnets afrundede hjørner eller hjørner, ændringer i maskinværktøjets acceleration, ændringer i værktøjets skæreretning og -vinkel, skærevibrationer osv., hvilket resulterer i problemer med kanten af grafitdelen. Hjørneskørhed og afskalning, alvorligt værktøjsslid og andre problemer. Især ved bearbejdning af hjørner og tynde og smalribbede grafitdele er det mere sandsynligt, at det forårsager hjørner og afskalning af emnet, hvilket også er blevet en vanskelighed ved grafitbearbejdning.
Grafitskæringsproces
De traditionelle bearbejdningsmetoder til grafitmaterialer omfatter drejning, fræsning, slibning, savning osv., men de kan kun realisere bearbejdning af grafitdele med simple former og lav præcision. Med den hurtige udvikling og anvendelse af grafit-højhastighedsbearbejdningscentre, skæreværktøjer og relaterede understøttende teknologier er disse traditionelle bearbejdningsmetoder gradvist blevet erstattet af højhastighedsbearbejdningsteknologier. Praksis har vist, at: på grund af grafits hårde og sprøde egenskaber er værktøjsslid mere alvorligt under bearbejdning, derfor anbefales det at bruge hårdmetal- eller diamantbelagte værktøjer.
Målinger i skæreprocessen
På grund af grafittens særlige egenskaber skal der træffes passende procesforanstaltninger for at opnå højkvalitetsbearbejdning af grafitdele. Ved grovbearbejdning af grafitmateriale kan værktøjet fremføres direkte på emnet med relativt store skæreparametre; for at undgå afskalning under sletbearbejdning anvendes ofte værktøjer med god slidstyrke for at reducere værktøjets skæremængde, og det skal sikres, at skæreværktøjets stigning er mindre end 1/2 af værktøjets diameter, og der skal udføres procesforanstaltninger såsom decelerationsbehandling ved bearbejdning i begge ender [4].
Det er også nødvendigt at arrangere skærebanen på en rimelig måde under skæring. Ved bearbejdning af den indre kontur bør den omgivende kontur udnyttes så meget som muligt for at skære den kraftfulde del af den skårne del, så den altid er tykkere og stærkere, og for at forhindre emnet i at knække [5]. Ved bearbejdning af planer eller riller skal du vælge diagonal eller spiralfremføring så meget som muligt; undgå øer på emnets arbejdsflade, og undgå at skære emnet af på arbejdsfladen.
Derudover er skæremetoden også en vigtig faktor, der påvirker grafitskæring. Skærevibrationerne under medfræsning er mindre end ved opfræsning. Værktøjets skæretykkelse under medfræsning reduceres fra det maksimale til nul, og der vil ikke være noget hoppefænomen, efter at værktøjet skærer ind i emnet. Derfor vælges medfræsning generelt til grafitbearbejdning.
Ved bearbejdning af grafitemner med komplekse strukturer skal der, udover at optimere bearbejdningsteknologien baseret på ovenstående overvejelser, træffes nogle særlige foranstaltninger i henhold til de specifikke forhold for at opnå de bedste skæreresultater.
Opslagstidspunkt: 20. feb. 2021